By mixing various materials, we can create new materials that are more durable than the materials they’re made of. GRP grating is one such material. GRP is an acronym for glass reinforced plastic grating, and it is essentially a material that has a lot of properties.
These properties are exactly why GRP is an essential item across many industries. The range of applications for this material is truly wide. While we will get into that, let’s explain what GRP grating actually is.
What Is GRP Grating?
Glass reinforced plastic grating is one of the most versatile materials out there. GRP is also commonly known as fiberglass composite plastic or FRP in short. Some of the properties of GRP include more flexibility, durability, lightweight, and strong resistance to high temperatures. Since the material is essentially a better version than fiberglass, it will not melt under high temperatures. Instead, it will burn. However, this is where the flexibility of the material kicks in.
You can make GRP even more resistant to high temperatures. The durability of the material is so strong that many industries use it as a substitute for steel. Since steel can catch corrosion, it creates a problem that many industries need to address. The answer comes in the form of glass reinforced plastic. GRP has strong chemical and corrosion resistance and is very easy to shape.
With plenty of more properties to highlight the effectiveness of GRP, let’s go over some of the common uses for the material.
Common Uses For GRP Grating
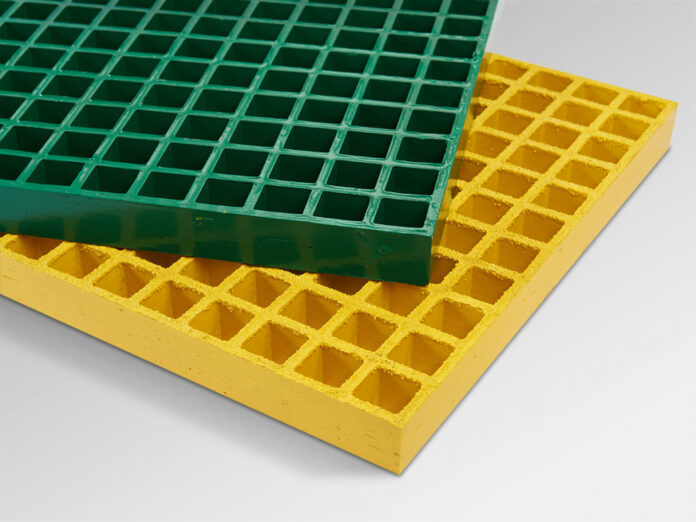
As mentioned previously, GRP grating can be used across many industries and in a variety of situations. The properties are the sole reason why GRP is so commonly used to replace steel.
Unlike steel, GRP is very lightweight and doesn’t corrode. In addition, it is more durable and performs much better under various metrics. The fact that you can shape GRP is another reason why it is so commonly used. GRP manufacturers can cut the material into specific shapes to fit the needs of many industries.
Let’s go over some of the most unique and common uses for GRP grating.
For Gullies and Gutters
One property that we failed to mention is that GRP grating is water-resistant. When you walk over the material in a wet environment, it gives you enough grip so you won’t slip. Because of that, many industries use the material as a walking surface. These industries operate with liquids, and some of the most common ones include the brewing industry, the marine industry, fisheries, and more.
By constructing trenches and gutters, workers can safely operate factories and harbors without fear of slipping. This is a major bonus for these industries, as it prevents work accidents and injuries. GRP grating adds so much grip to walking surfaces that many other industries that operate with liquids slowly incorporate it.
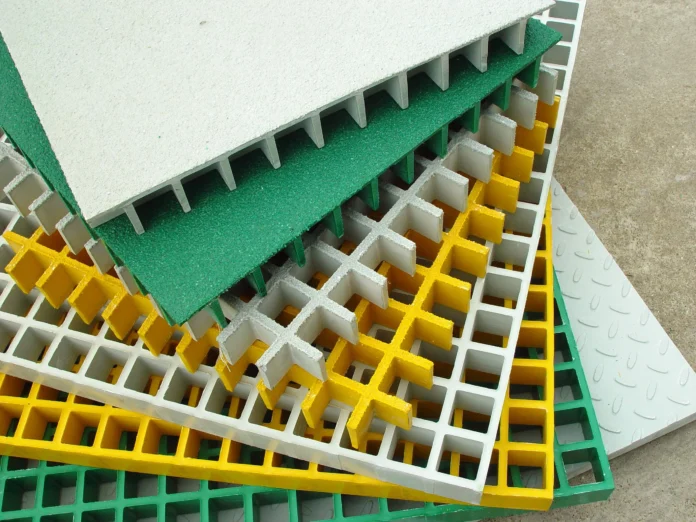
For Ramps, Walkways, Stairs, and Platforms
We circle back to the previous point and the fact that GRP grating is water-resistant, which adds grip when a person is walking over a wet surface. This makes it important for walkways and ramps due to the safety factor. But not just that, construction firms use GRP grating to create specialized platforms that assist them when working on construction sites.
Since the goal is to minimize risk and maximize safety, it makes the material a necessity in the construction industry. Since water can corrode metal and various other materials, GRP grating will last much longer. When you add the material to ramps, walkways, stairs, and platforms, it increases the lifespan of these walking surfaces.
In addition to all that, GRP grating systems are used for rails, stairs, fencing, decking, and much more.
If you’re interested in learning more about specialized GRP grating systems, make sure to visit https://www.grpgratingsystems.co.uk.
For Offshore Installations
Many offshore industries need to deal with the elements and the environment that they operate in. Oil rigs, ships, and similar installations are constantly at odds with water and wind. This makes working on such installations rather difficult.
So there’s a need for a material that can deal with high winds, high and low temperatures, and deal when submerged into the water without corroding. That material is GRP grating. GRP grating can be added to oil rigs or ships to enhance the durability and corrosion resistance of said installations.
The fact that the material is super lightweight makes transportation a piece of cake. But even more so, coating various parts of a ship or oil rig with the material will make it easier to deal with water. Namely, some of these industries coat entire machines with the material and submerge them. This includes smaller boats, tools, items for repair crews, and more.
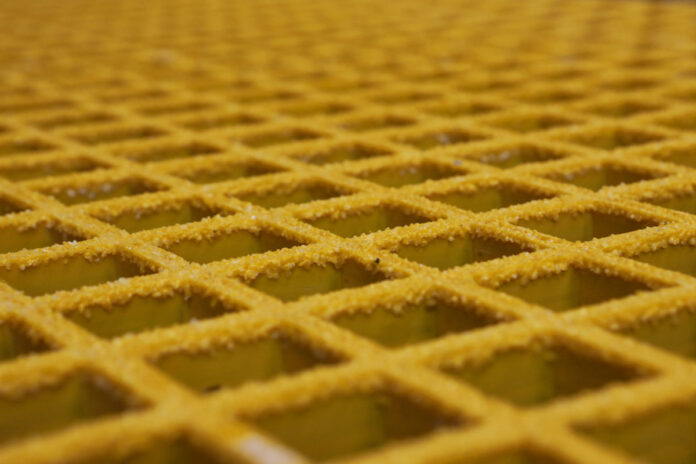
Why Should You Replace Steel Grating With GRP Grating?
So far we’ve talked extensively about the many properties of GRP grating. Before this material existed, steel grating was the obvious choice for many industries.
But now that GRP is a thing, here are a few reasons why you should switch to it.
Rust-Proof, Impact Resistance, More Strength
Rust can cause a lot of issues in the workplace. Industries that rely on water as a source for production understand the importance of rust-proofing tools and items. Heavy industries are prime examples of this. Corrosion can be such an issue in a heavy industrial setting that companies could lose tens of thousands of dollars if steel flooring or platforms catch rust.
By coating with GRP, you eliminate the problem. But it’s not just fluids that can derail an entire operation if corrosion becomes an issue. Chemicals can also impact machinery and applications in a variety of ways. It can even impact the lives of people.
By using GRP coating, you also get a material that has high structural integrity. Even if you drop something on a GRP grated floor, it will stay intact. And lastly, although certainly not the least why you should prioritize GRP grating over steel grating is the fact that you get a material that is equally stronger but significantly lighter. Put two and two together and GRP is a better option.