One of the integral parts of mould repair and maintenance is welding. When dealing with mold, you must ensure you have the right team to help in welding. Further, it’s important to note that the results of the process depend on the level of difficulty, welder skill, machine capability, and communication. Mold repair welding includes laser, tungsten inert gas, and Micro Tig Welding. It’s crucial to note that some companies, such as Micro Weld, Inc have extraordinary evidence in all three processes, while others specialize in one. When looking for a welder, you must ensure they are reputable and experienced. They should fully understand customer expectations and inform the customer about the considerations and risks involved before the welding begins. It’s essential to note that it cannot be unwelded once something is welded. Any mistake committed must be machined away for a fresh start. This article will explore vital considerations for mold repair welding.
Essential Questions that Must Be Asked when Preparing for Optimal Mold Repair
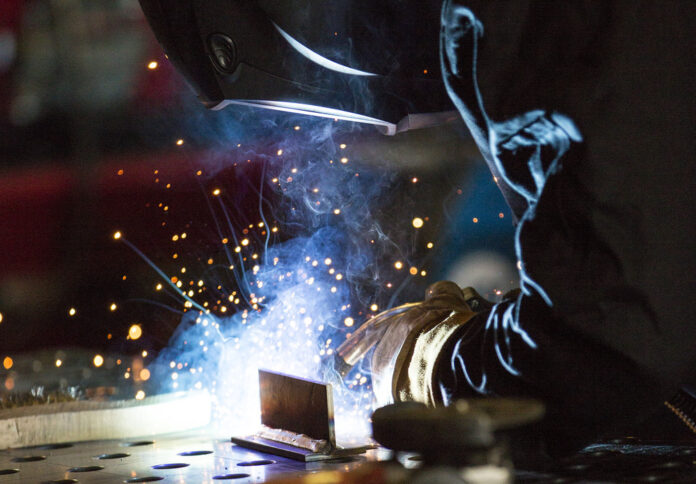
It’s important to note that every repair job is unique to the welder. Some jobs will require different hand positions, movement, and machine calibration. This means that everyone involved should be on the same page. As the job owner, never assume that the welder knows what you want. Most mold can be due to inoperability due to damage and engineering changes. Below as some of the questions that the welder needs to ask
What am I welding?
A welder should ask this question to understand better what is required of them. The mold maker will state their requirements to get the tool running. Further, they need to understand what the mold maker does not want.
Where am I welding?
The welder must know the exact location of the repair to make the type of equipment they will need to carry. In some areas, they require the TIG-welding torch or a laser-welding head.
Some of the Critical Considerations
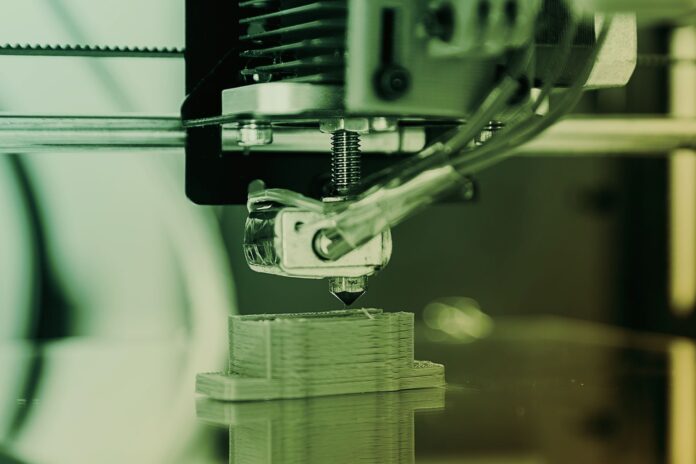
The Size
The mold size is crucial as it helps dictate the appropriate strategy to be used in the welding process. The laser welder is fixed and cannot be moved, making it vital to position it precisely beneath the laser head. This can limit the size of the mold to be repaired. Large laser welders with movable arms are available to help better access the mold. On the other hand, the TIG welding torch can be moved around and positioned on the wrist or arm. This increases mobility and eases the welding of large molds.
Time
It’s crucial to note that laser welding takes longer than micro-TIG welding since the lasers require a fixed position. However, the process reduces distortion and creates more minor welds. The micro-TIG welding can help produce more extensive weld deposits faster and more effectively. The problem can be weld sink around the heat-affected zone. The sink can occur when the weld cools too rapidly, causing a ring of depression around the area where the weld meets.
End Note
The above are crucial considerations that you need to make when considering mold repair welding. It’s essential to consider the best process depending on the type and extent of the mold.