The pouring of metal into a mold is only one step of the casting process. In order for the metal to be poured, it must first be melted. And, as you can probably tell, melting metal isn’t as simple as lighting the fire underneath it and letting it melt. In fact, the process is very complex, and something as “simple” as simply melting down some iron can be done in numerous ways.
And, it all starts with four types of furnaces!
What Furnaces Can You Use To Melt Metal?
There are four main types of melting furnaces used in metal casting: cupola furnaces, crucible furnaces, induction furnaces, and electric arc furnaces. Each has its own advantages and disadvantages that make it more or less suitable for certain applications.
Cupola Furnace
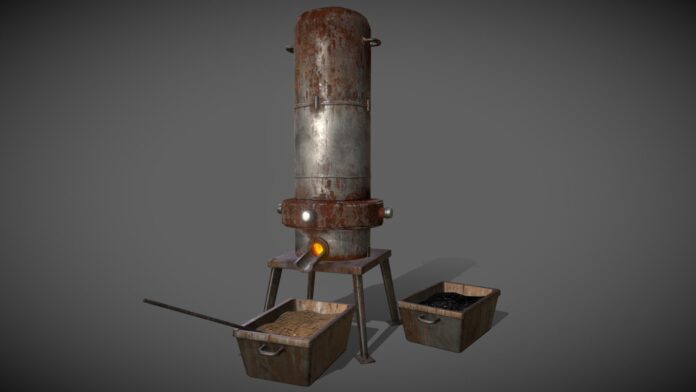
The cupola furnace is the most common type of melting furnace used in iron casting. It is a vertical cylinder lined with refractory material, through which coal-coke and iron are fed. Air is blown through the bottom of the cupola, causing the coke to ignite and heat the iron. The hot iron melts and collects in the bottom of the furnace, from where it is periodically tapped off. However, there are mostly out of use at this point.
Crucible Furnace
The crucible furnace is a type of melting furnace that uses a ceramic vessel, called a crucible, to contain the metal being melted. The crucible is placed inside a furnace and heated to the melting point of the metal.
Induction Furnace
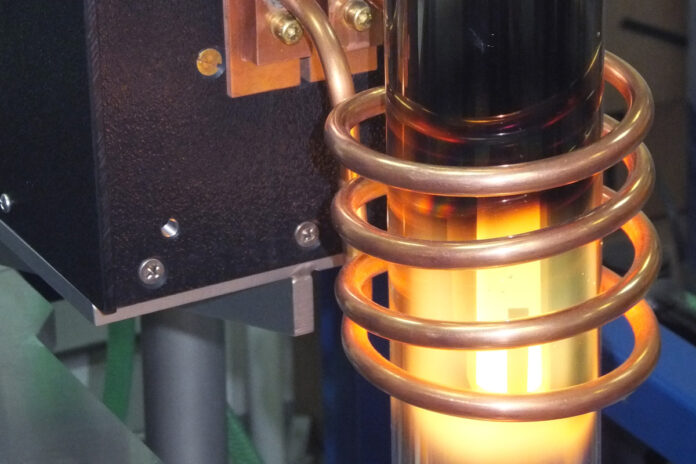
The induction furnace uses an electromagnetic field to heat the metal. A copper coil carrying an alternating current surrounds the furnace, causing an electromagnetic field to be generated. When the furnace is turned on, alternating currents create a powerful reversing magnetic field, causing it to heat up and melt the contents of the furnace.
Electric Arc Furnace
Electric arc furnaces (EAF) are a type of furnace that melts metal using high-voltage electricity. The metal is melted by passing an electrical current through it, which creates an arc of electricity between two electrodes. This process is more efficient than adding external heat when melting large volumes of metal at one time and can hold up to 400 tons of steel, which is one of the main reasons why these are the number one option for metal melting today.
Why Do You Need To Melt Metal For Casting?
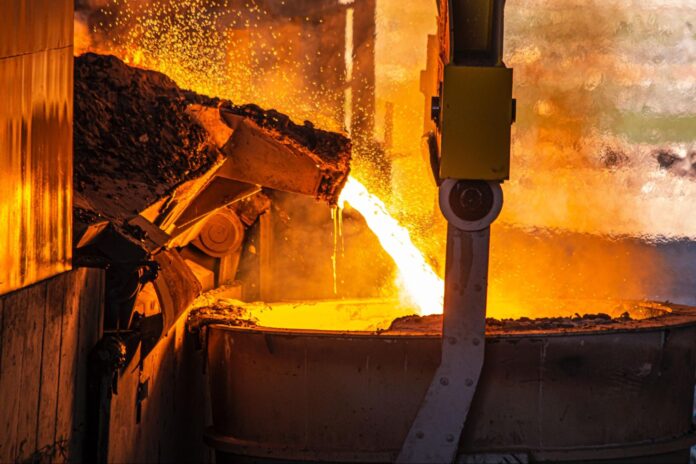
Melting is an essential step in the casting process because it allows for the metal to be poured into a mold. When metal is cast, it is first melted and then poured into a mold where it takes the shape of the mold as it cools and solidifies.
As you know, there are a variety of metals that can be melted for casting, including iron, steel, aluminum, brass, etc. Each has its own melting point, which must be reached in order to melt it and begin the casting process. And, how do you do that?
Well, generally, the steps involved in melting depend on the type of furnace being used. However, there are usually three steps you have to go through:
- The metal is placed in the furnace
- The furnace is heated to the melting point of the metal
- The molten metal is poured out of the furnace for casting
Naturally, this process is not without its drawbacks. In fact, there’s quite a bit of waste and pollution going on with this process, but that’s inevitable. And, since it’s inevitable, we don’t really see the point in boring you with it, but if you’re really interested in what kind of waste is produced during the casting process, you may click here and find out.
We, on the other hand, will move on to the bigger picture – the entire casting process.
What Does The Metal Casting Process Look Like?
The casting process generally consists of the following steps:
Creating The Mold
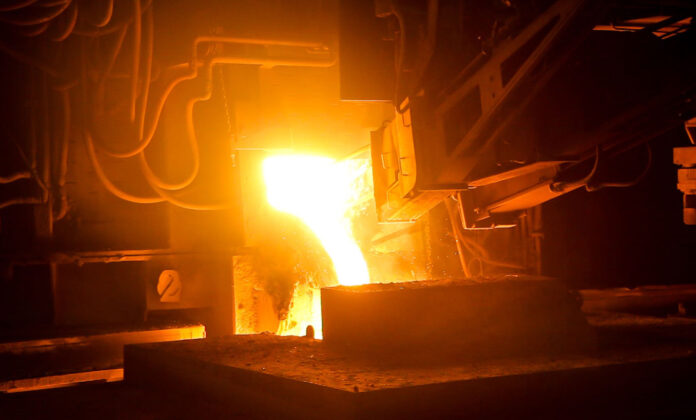
There are two main ways to create a mold: using a pattern or using a negative impression.
A pattern is an object that is used to create a negative impression of the desired shape in the mold material. Once the impression has been made, the pattern is removed and the cavity that it created is used to pour the molten metal.
A negative impression is made by pressing the object that you wish to cast into a molding material. Once the object has been removed, the cavity that it left behind is used to pour the molten metal.
Both of these methods have their own advantages and disadvantages, which we won’t get into details about. For now, just know that either method can be used to create a mold for casting.
Filling The Mold
Well, there’s actually a step before this one, but we’ve covered the melting process already, so let’s just move on.
Once the mold has been created, it is filled with molten metal. This is generally done using a ladle, but can also be done using gravity if the mold is placed on a higher level than the furnace.
The molten metal is poured into the mold until it is completely full. It is important to make sure that the mold is filled completely in order to avoid any defects in the final casting.
Cooling And Solidifying
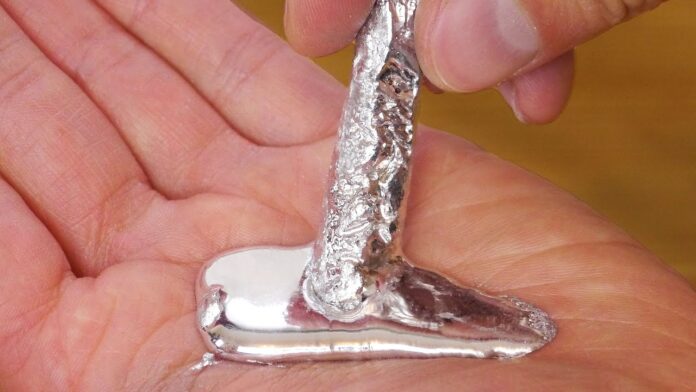
Once the mold has been filled with molten metal, it is allowed to cool and solidify. The length of time that this takes depends on the type of metal being used as well as the size and shape of the casting.
Smaller castings made from metals with a high melting point, such as steel, will take longer to cool and solidify than larger castings made from metals with a lower melting point, such as aluminum.
The cooling process can be sped up by using a coolant, such as water.
Opening The Mold And Removing The Casting
Once the metal has cooled and solidified in the mold, it is opened and the casting is removed.
The mold can be opened manually or with the help of machinery, depending on the size and weight of it. The casting is then removed and any excess material is trimmed away.
Cleaning And Finishing The Casting
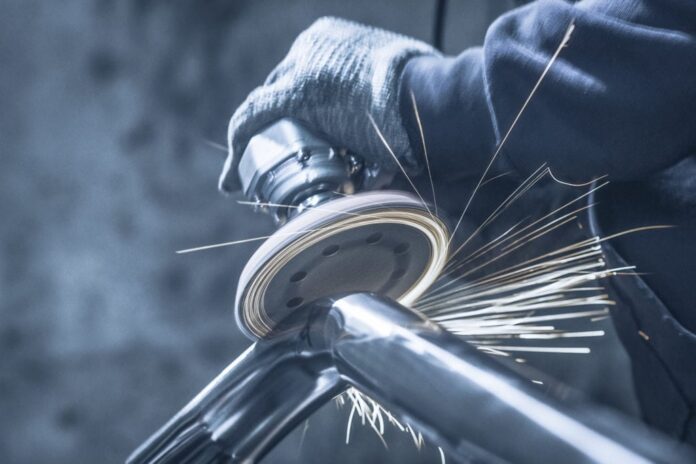
The final step in the metal casting process is cleaning and finishing the casting. This step is necessary in order to remove any debris or imperfections that may be present on the surface of the casting.
Cleaning can be done manually or with the help of machinery, just like in the previous step. Once the casting has been cleaned – it is then finished as necessary. This may involve machining, polishing, painting, or plating, depending on the intended use of the casting.
Conclusion
And that’s it! That’s the metal melting and casting process in a nutshell. Of course, there are many different types of casting and each one has its own unique steps and procedures.
But, the steps that we’ve outlined here are the basics that are involved in all types of casting. So, now you know how metal is melted and cast into the various objects that we use in our everyday lives.