A pharmaceutical unit faces several potential hazards daily. The heavy use of chemicals and heavy equipment poses a constant risk to the health and well-being of personnel who work in pharma units. Moreover, the safety of the product itself is a major concern for drug manufacturers.
Global regulatory bodies like the WHO, the FDA, and the pharmacopeia commissions of various countries have strict norms for drug safety. So ensuring that the absence of contaminants and the fidelity of measurements when it comes to drug composition is given high priority.
Pieces Of Equipment That You Will See At A Drug Manufacturing Unit
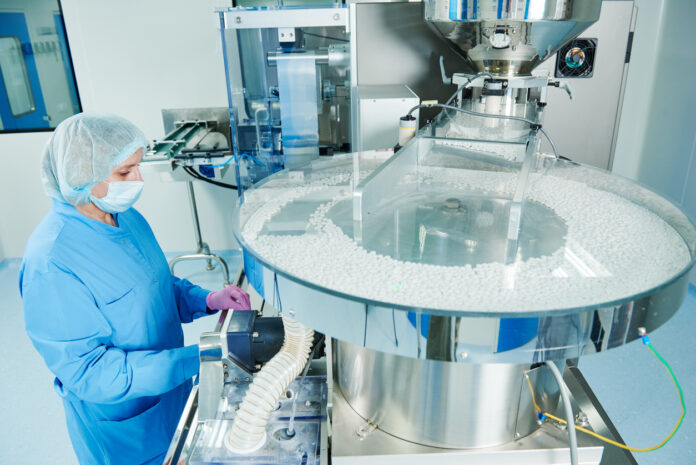
In this article, you will come across several pieces of equipment that are present in a drug manufacturing unit that contributes to the unit’s adherence to Good manufacturing practices. WHO’s Good manufacturing practices (GMPs) give quality assurance to customers who are buying and consuming medicines.
Hence, all manufacturers pay utmost attention to GMPs as it directly affects their reputation and marketing ability.
Equipment Used In The Manufacturing Of Drugs
Centrifuges And Freezers
Several machines are required in the manufacturing process of drugs. However, the centrifuge and the freezers are probably the most important of the lot. A centrifuge is a device that separates the components of a fluid based on its densities. It is required to separate impurities or by-products while manufacturing drugs.
Freezers are machines that keep things warm. Many chemicals, especially those with proteins, degrade when exposed to heat. So freezers help keep the integrity of the medicines intact.
Equipment That Is Used In Manufacturing And Packaging
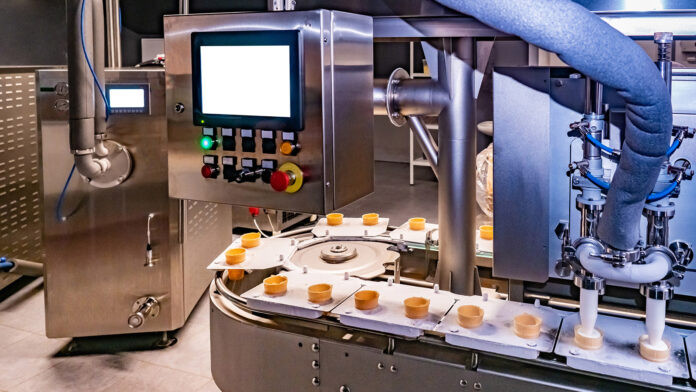
Pharmaceutical Packaging Machinery
A pharmaceutical packaging machinery is a comprehensive equipment that takes care of all aspects of medicine packaging. Most modern pharmaceutical packaging machinery includes sealers, label applicators, etc.
Most packaging units are flexible to pack different dosages of the same medicine. They have weight equipment and can be automated to fill in the precise weight or volume of the drug in a capsule.
A Liquid Capsule Filling Machine
Not all capsules contain a solid or a powder as their principal component. In such cases, manufacturers use a liquid capsule-filling machine. These machines are automated units that allow tamper-proof filling of liquid and semi-solid APIs in definite dosages.
APIs or active pharmaceutical ingredients are the principal components that give the drug its functionality. Many APIs are very sensitive to the presence of contaminants, such as traces of other chemicals.
Most modern liquid capsule-filling machines have outstanding cleanability. So having a liquid capsule filling unit is a guarantee that the chances of accidental contamination will be minimal.
A Powder Filling Unit
A powder filling unit is another essential component of a drug manufacturing plant. Powder fillers can be of different types, like fillers that fill powder based on the net weight, then there are fillers that are known as cup fillers.
The cup fillers use the volume of a powder instead of its weight as a measure while filling different units.
Each type of filler has some instinctive advantages. For instance, the net weight fillers are very accurate, and they are suitable for handling components that have an irregular (amorphous) shape. On the other hand, cup filters have a simple design and are inexpensive. However, they are not recommended for very fine powders.
Equipment That Is Used To Maintain The Safety Of Personnel
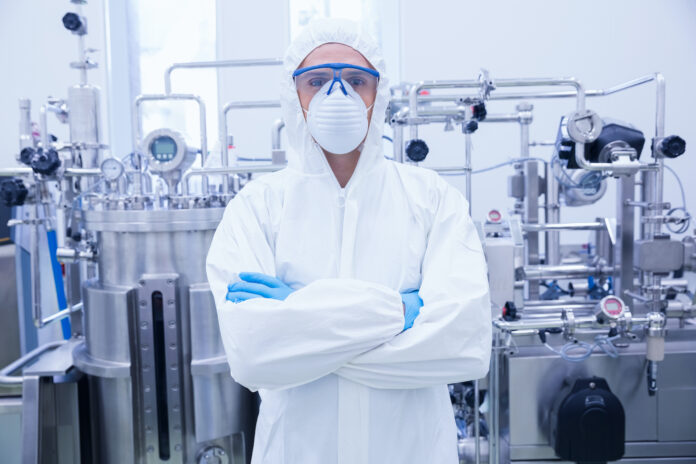
The people who work in drug manufacturing units are exposed to a considerable amount of risk. Below is a list of risks in a drug manufacturing unit and the ways to mitigate those risks.
- Airborne Hazards-Airborne hazards are the most difficult to deal with simply because you cannot see the hazard-causing substance. Most often, when the API is being powdered, gasses and vapors escape into the atmosphere.
APIs consist of potent chemicals which have varied effects on the human body. When personnel working in a drug manufacturing unit inhale excessive amounts of any API, it is a cause of great concern.
Such protective equipment as gas masks or PPE kits is essential to ensure the safety of the people working in a drug manufacturing unit.
- Fire Hazards or chances of an explosion- Fire hazards in combustible dust and flammable gasses may be generated in a drug manufacturing unit. The situation becomes grave when the manufacturing unit has enclosed places with improper ventilation.
The most effective way to prevent fire hazards is to make the personnel aware of safety rules and conduct fire evacuation drills at regular intervals. Apart from this, fire extinguishers must be present throughout the premises, and the electricity supply network must be regularly monitored for damaged wires.
- Hazards from accidental falls- At any manufacturing unit, personnel may have to work at a height. So falls can cause injuries and even fatalities in a drug manufacturing unit. So in order to prevent accidental falls, proper fencing, and sign boards are a must.
- Hazards caused due to skin contact with chemicals- Human skin should in no way come in direct contact with APIs. The human skin can react adversely to chemical agents. Also, the drug formulation’s purity may be compromised when it comes in contact with human skin.
The human skin hosts a plethora of microorganisms like bacteria and fungi, and if a person’s hand comes in contact with a drug formulation, its efficacy may be seriously compromised.
Most personnel use gloves on their hands at all times when they handle APIs to prevent contamination of the drug formulations.
Conclusion
A unit that manufactures medicines has to give paramount importance to the safekeeping of its ingredients. Moreover, the measurements, packaging, etc., also must be tightly regulated to ensure the efficacy and safety of drugs.
Accidental contamination of drugs can have disastrous consequences. In minor cases, drug contamination can cause reversible damage. But in case of a significant breach, it can prove to be lethal. There have been instances of methadone poisoning in antibiotics in the past, and hence today, the legal norms for drug contamination have become quite strong and effective.